There are several types of demulsifiers that are soluble in oil. These demulsifiers are used in the desalting process to remove the salts from the oil. They can be either physical or chemical. The quality of the oil recovered from the desalting process is determined by the type of demulsifier and the method of its application.
Various Uses of Oil-Soluble Demulsifier
Oil-soluble demulsifiers are compounds that are formulated to break water-in-oil emulsions. They usually contain a carrier solvent, such as 2-ethylhexanol. The composition of the carrier solvent can have an effect on the cost and toxicity of the demulsifier.
The use of demulsifiers is a common step in oily sludge treatment. As a result of this process, the amount of oily sludge can be reduced. In addition to this, demulsifiers also help to separate water from crude oil. Increasing industrialization and rising demand for oil-related derivatives are expected to drive the global demulsifier market.
Demulsifiers are a class of specialty chemicals that are used to break water-in-oil sludge emulsions. These substances can be synthetic or organic. Their main applications are in oil and gas processing, lubricating oil products, and pharmaceutical industries.
Oil-soluble demulsifiers are formulated to remove saline water from crude oil prior to refining. Saline water can cause corrosion in pipelines and refining equipment. It can also create environmental problems. So, the need for efficient demulsification is paramount.
The oil-soluble demulsifier is soluble in crude oil, organic solvents such as toluene, benzene, ethanol, methanol, xylene, methylbenzene, aromatic other solvents.
The formulation of commercial demulsifiers is designed to yield materials that are more effective and universal. This involves a detailed process that includes characterizing the crude oil, obtaining a formulation, and evaluating it in the field.
Commercial demulsifiers are typically formulated with a combination of two to four chemicals, which are then mixed in a carrier solvent. Organic solvents, such as ethylene diamine, are frequently used in this formulation. However, the presence of these types of organic solvents can increase the cost and toxicity of the product.
Various studies have been conducted to investigate the mechanisms of emulsification. The key factors in the demulsification process include temperature, pressure, adsorption, and coalescence.
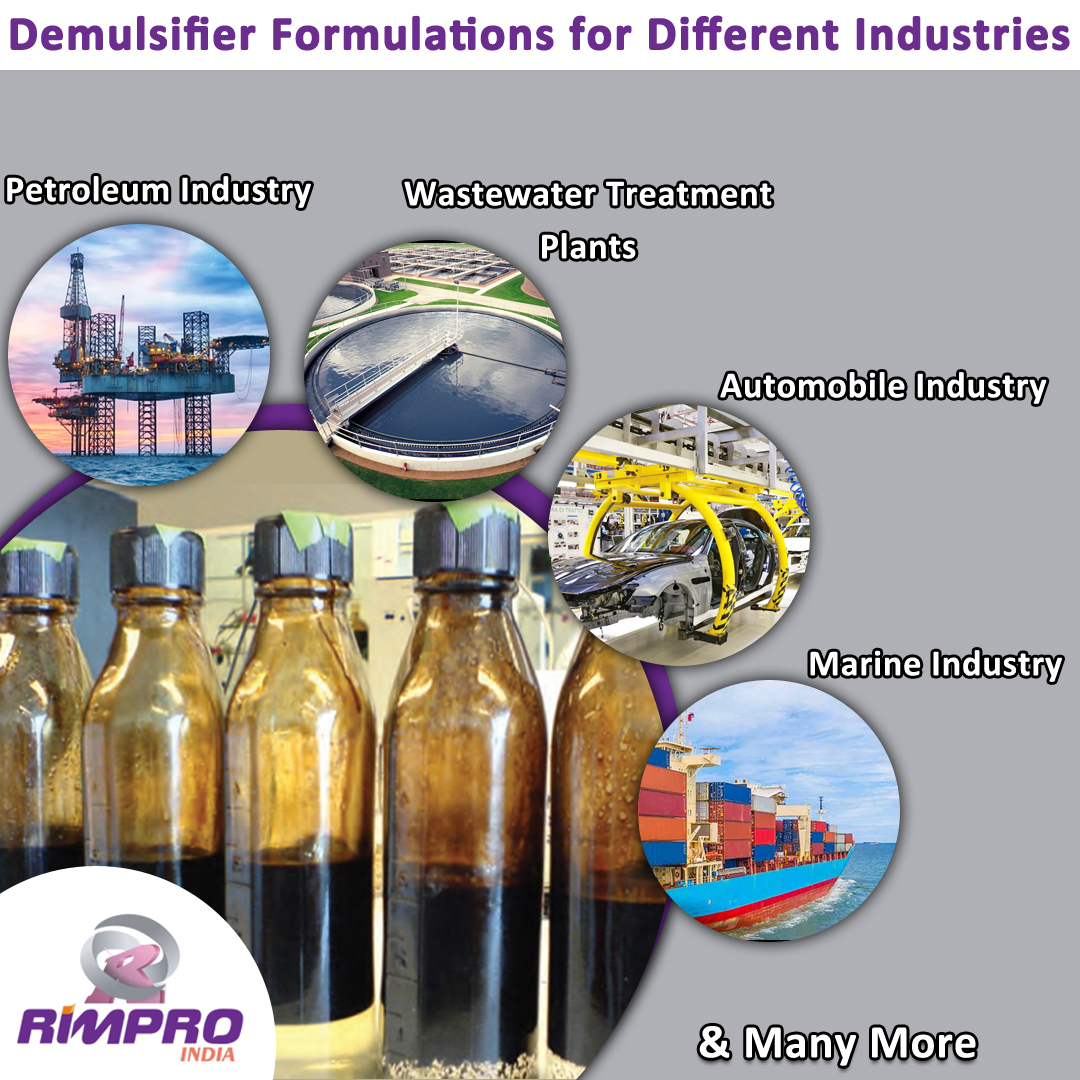
Physical Methods of Demulsification Process
Demulsification of crude oil emulsions has attracted considerable attention from the oilfield research community. This is because demulsification can maximize the profitability of oil production. It also minimizes the environmental impact of the process.
The effectiveness of a demulsifier depends on the interaction between the surfactant and the emulsion. There are many different types of demulsifiers. Some are organic while others are inorganic. They come in different concentrations, and their dosage depends on the type of emulsion and the amount of contaminant present.
Demulsification processes involve the introduction of a chemical additive to the emulsion. These additives are intended to speed up the breaking of the emulsion. To accomplish this, demulsifiers are typically added in a water-in-crude oil emulsion.
Demulsification of crude oil emulsions can be performed using several physical methods. For instance, an alternating electric current can be used to break up the emulsion. In contrast, microwave heating can be employed.
Electrical demulsification has been applied in various industrial processes. One example of this technique is the treatment of paint manufacturing effluents. Another example is the production of oilfield produced water.
Electrical demulsification involves the application of a high-voltage alternating current in the emulsion. This enables the rapid fusion of small water droplets, and the re-arrangement of polar molecules. A pulsatile electric field has also been used. However, PEF has been shown to suppress the formation of secondary droplets in the low-frequency electric domain.
Other methods of chemical demulsification include steam injection, caustic injection, and combustion. These techniques can produce viscous emulsions. As a result, the demulsifier dosage needs to be controlled carefully.
Physical methods of demulsifier formulation have been investigated in the laboratory and in the field. Among the factors that affect the demulsification rate are the adsorption of the demulsifier at the surface of the emulsion, the interfacial viscosity, the film thinning behaviour of the demulsifier, and the density of the emulsion.
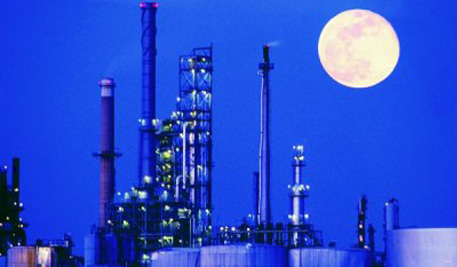
Chemical Agents to Overcome Barrier of Demulsification Formation
Demulsification is the process of separating oil and water by using chemical agents to overcome the barrier in the formula. The formulation is usually a mixture of several agents. These are usually inorganic or organic. A number of different demulsifiers are available, each containing a different range of concentrations.
In order to achieve optimal emulsion breaking, a demulsifier must be properly selected and mixed. This includes a suitable dosage level and adequate agitation. Additionally, the quality of the interface fluids is important. Typically, these will include water, hydrocarbons, asphaltenes, and inorganic solids.
Oil-soluble demulsifiers are typically formulated in organic solvents such as diethylene triamine. They may also be composed of oxyalkylated alkyl phenols, bisphenol glycol ethers, and oxyalkylated amines.
Formulations of the present invention are capable of breaking hydrocarbon emulsions derived from refined mineral oils, gasoline, and crude oil. They are advantageously suited for breaking polar crude oils, which are usually characterized by high aromatic content and low paraffins.
Demulsifiers can also be used for tertiary oil recovery. Because the amount of asphaltenes and inorganic solids is lower in these formulations, the use of these demulsifiers can reduce the final disposal cost.
Demulsifiers are often classified according to their molecular weight, which is a metric that compares their adsorption capacity onto the water/oil interface. High-molecular-weight demulsifiers are often able to decrease the interfacial tension between the two media. Low-molecular-weight demulsifiers also reduce the interfacial tension but adsorb to a greater degree.
Optimal emulsion breaking with demulsifiers requires adequate mixing of the chemical, a sufficient retention time in the separator, and proper agitation. A record of the operational data will be necessary in order to assess the performance. It will also include the operating temperatures, pressures, production rates, sampling locations, and the equipment used for dilution and dosing.
When using chemical demulsifiers, the added point is very critical. While the exact demulsification rates will vary with various system conditions, the added point generally needs to be at least 30 to 50% higher than the minimum rate required to operate the system at its best.
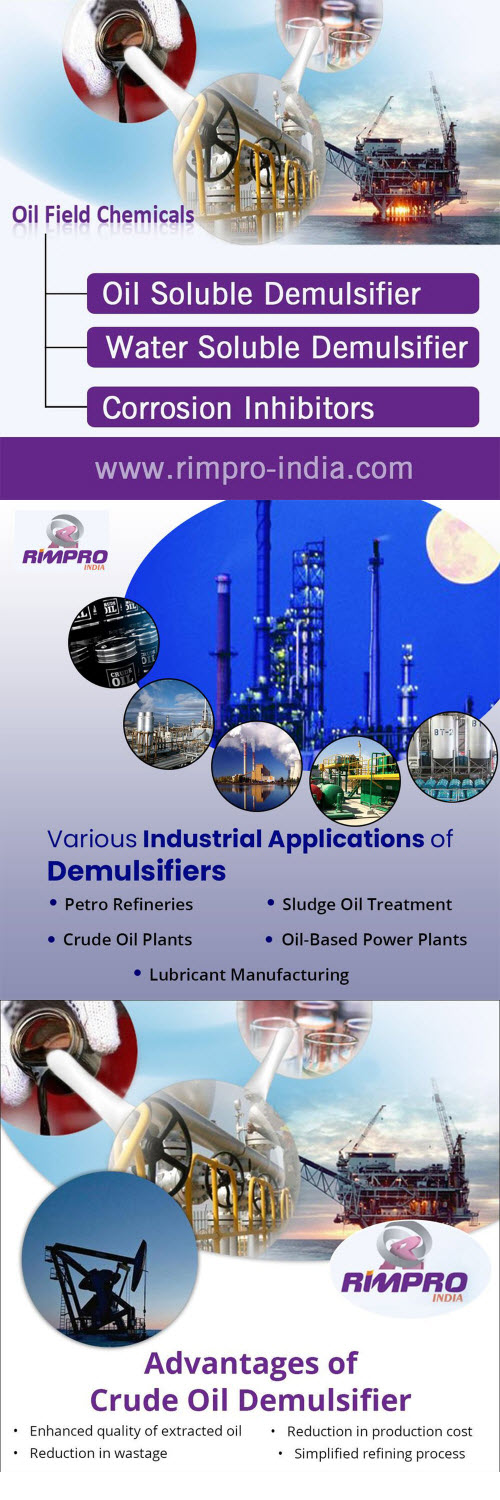
Oil Quality Recovered from Desalting Process
A refinery is a facility that handles various types of crude oil, using chemical processes to remove contaminants. The process involves the recycling of crude into various straight-run cuts, and then separation of these into various fractions. During this process, a unit known as a desalting unit is used. This unit concentrates suspended water globules from the crude, and then filters them through a diatomaceous earth layer. Afterward, the crude is sent to a crude distillation tower. If the process is done incorrectly, there can be a variety of problems, including fouling of heater tubes, clogging of the heaters, and causing fires. In addition, if the unit leaks, low boiling point components of the crude may be released. Ultimately, this process can reduce the quality of oil recovered from the crude.
There are several ways of desalting crude, and some of them use sulfuric acid. Other methods, such as electrostatic desalting, utilize high voltage electrostatic charges to isolate globules from the crude. Usually, a surfactant is added only when there is a large number of suspended solids in the crude.