Corrosion inhibitors play a vital role in protecting industrial equipment and infrastructure from the detrimental effects of corrosion. Effective management and maintenance of corrosion inhibitor systems are essential to ensure long-term protection and optimal performance. In this article, we will discuss best practices for managing and maintaining corrosion inhibitor systems, including strategies for monitoring performance, conducting routine inspections, and optimizing dosage rates.
Understanding Corrosion Inhibitors
Corrosion inhibitors are chemical substances that, when added to corrosive environments, form a protective layer on metal surfaces, thereby reducing the rate of corrosion. These inhibitors can be applied in various forms, including liquids, powders, and coatings, and are commonly used in industries such as oil and gas, manufacturing, and water treatment.
Monitoring Performance
Regular monitoring of corrosion inhibitor performance is critical to ensuring continued protection against corrosion. This can be achieved through:
- Corrosion Rate Measurements: Conducting periodic corrosion rate measurements using techniques such as electrochemical corrosion monitoring or weight loss analysis provides insights into the effectiveness of the inhibitor system.
- Chemical Analysis: Analyzing samples of the corrosion inhibitor solution for chemical composition and concentration helps ensure that the inhibitor is present at the desired levels.
- Visual Inspections: Visual inspections of equipment and infrastructure for signs of corrosion, such as rust formation or pitting, can indicate potential issues with the inhibitor system.
Conducting Routine Inspections
Routine inspections are essential for identifying any issues with the corrosion inhibitor system and implementing corrective actions. Key aspects of routine inspections include:
- Visual Examination: Regular visual inspections of equipment and infrastructure to detect signs of corrosion, leaks, or damage.
- Functional Testing: Testing the functionality of corrosion inhibitor injection systems, monitoring equipment, and associated control systems to ensure proper operation.
- Documentation: Maintaining detailed records of inspection findings, including any corrective actions taken and recommendations for future maintenance.
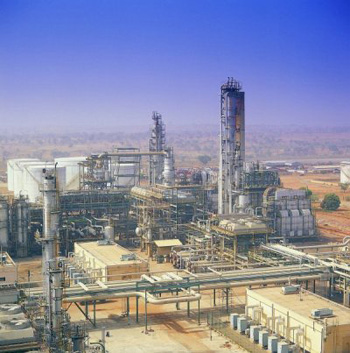
Optimizing Dosage Rates
Optimizing corrosion inhibitor dosage rates is crucial for achieving effective corrosion protection while minimizing costs and environmental impact. Factors to consider when optimizing dosage rates include:
- Corrosion Environment: Assessing the severity of the corrosion environment and adjusting inhibitor dosage rates accordingly.
- Water Chemistry: Monitoring water chemistry parameters such as pH, alkalinity, and hardness to determine the appropriate inhibitor dosage for optimal performance.
- Inhibitor Compatibility: Ensuring compatibility between the corrosion inhibitor and other chemicals present in the system to prevent adverse reactions and maintain effectiveness.
Conclusion
Effective management and maintenance of corrosion inhibitor systems are essential for protecting industrial equipment and infrastructure from corrosion. By implementing best practices for monitoring performance, conducting routine inspections, and optimizing dosage rates, companies can ensure long-term corrosion protection and maximize the lifespan of their assets.