Chemical processing plays a crucial role in various industries, ranging from oil and gas to pharmaceuticals. One of the significant challenges faced in these processes is the presence of emulsions, which are stable mixtures of immiscible liquids. Emulsions can negatively impact process efficiency and product quality. To overcome this challenge, demulsifiers are employed.
Emulsions occur when two or more immiscible liquids, such as oil and water, are combined and stabilized by surfactants or colloidal particles. These mixtures can pose problems in chemical processing, causing issues such as reduced separation efficiency, increased corrosion, and product quality deterioration. Demulsification, on the other hand, is the process of breaking down emulsions into their constituent phases for efficient separation.
Challenges in Chemical Processing
Chemical processing involves various operations, such as extraction, separation, and purification. However, emulsions can disrupt these processes, leading to increased costs and decreased productivity. Some common challenges faced in chemical processing include prolonged phase separation, increased equipment fouling, reduced product purity, and compromised process stability.
The Need for Demulsifiers in Chemical Processing
Demulsifiers play a vital role in chemical processing by facilitating the separation of emulsions into their individual liquid phases. They contain active agents that disrupt the emulsion structure, allowing for efficient phase separation. Demulsifiers help mitigate the challenges associated with emulsions, enhancing process efficiency, and improving product quality.
Types of Demulsifiers
Demulsifiers can be classified into different types based on their chemical composition and mode of action. Some common types include surfactant-based demulsifiers, polymeric demulsifiers, and natural demulsifiers derived from plant or animal sources. Each type has its unique characteristics and applications, making them suitable for specific emulsion systems.
Mechanisms of Demulsification
Demulsifiers function through various mechanisms to destabilize emulsions and promote phase separation. These mechanisms include adsorption at the oil-water interface, coalescence of dispersed droplets, and prevention of re-emulsification. The choice of demulsifier and its mechanism of action depends on the emulsion type, temperature, and other process parameters.
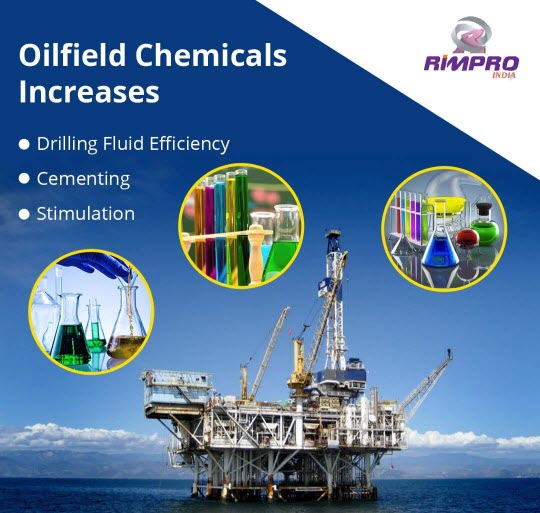
Factors Affecting Demulsifier Performance
Several factors influence the performance of demulsifiers in chemical processing. These include emulsion stability, temperature, pH, salinity, demulsifier concentration, and contact time. Understanding these factors and their interplay is essential for selecting the appropriate demulsifier and optimizing its performance in specific applications.
Application of Demulsifiers in Various Industries
Demulsifiers find applications in diverse industries, including oil and gas, petrochemicals, pharmaceuticals, and wastewater treatment. In the oil and gas sector, demulsifiers are used to separate crude oil from water, improving oil recovery and reducing production costs. In petrochemical plants, demulsifiers aid in the separation of hydrocarbon mixtures, ensuring the purity of the final products. The pharmaceutical industry utilizes demulsifiers for the extraction and purification of active pharmaceutical ingredients. Additionally, demulsifiers are valuable in wastewater treatment processes, where they assist in removing oil and suspended solids from water.
Benefits and Limitations of Demulsifiers
Demulsifiers offer several benefits in chemical processing. They enhance separation efficiency, reduce processing time, minimize equipment fouling, and improve product quality. By facilitating the effective separation of emulsions, demulsifiers help companies achieve higher yields, optimize resource utilization, and meet stringent regulatory requirements. However, it is important to note that demulsifiers may have limitations in certain situations, such as when dealing with highly stable emulsions or in environments with extreme operating conditions.
Best Practices for Demulsifier Selection and Usage
Selecting the right demulsifier for a specific application is crucial for achieving optimal results. It involves considering factors such as the emulsion composition, process conditions, and desired separation efficiency. Conducting thorough laboratory tests and pilot studies can help in evaluating demulsifier performance before full-scale implementation. Additionally, proper demulsifier dosing, adequate mixing, and regular monitoring of process parameters are essential for maximizing demulsification efficiency.
Environmental Considerations
With increasing awareness about environmental sustainability, the selection and use of demulsifiers also involve environmental considerations. Companies are encouraged to choose demulsifiers that are environmentally friendly, biodegradable, and have low toxicity. Additionally, implementing efficient wastewater treatment processes can minimize the environmental impact associated with demulsifier usage.