Demulsification plays a crucial role in various industries, where the separation of oil and water emulsions is vital for efficient operations. However, this process often encounters common challenges that hinder the desired separation.
Demulsification is the process of breaking down emulsions into their individual components, typically oil and water. Emulsions occur when immiscible liquids are dispersed in one another, forming a stable mixture. While emulsions can be beneficial in certain applications, such as in food and cosmetics, they can be problematic in industries like petroleum, wastewater treatment, and chemical manufacturing. In these contexts, the separation of oil and water is necessary for further processing or environmental considerations.
Common Problems in Demulsification
Emulsion stability: Emulsions can exhibit high stability, making it challenging to separate the oil and water phases. Factors such as surfactants, pH, temperature, and the presence of solids contribute to emulsion stability.
Slow separation: Inefficient separation processes can result in prolonged settling times, leading to reduced productivity and increased operational costs. Slow separation can occur due to various factors, including the type of emulsion, particle size distribution, and the absence of effective demulsifiers.
Difficulty in breaking water-in-oil emulsions: Water-in-oil emulsions, where water droplets are dispersed within the oil phase, are particularly problematic to break. The interfacial tension between water and oil, as well as the emulsion’s stability, must be overcome for successful separation.
Residual water content: After separation, traces of water may remain in the oil phase, adversely affecting its quality and performance. Achieving low residual water content is essential in applications where water presence is undesirable, such as fuel production or lubricant manufacturing.
High energy consumption: Demulsification processes often require significant energy inputs, such as heating or mechanical agitation, to facilitate separation. High energy consumption can lead to increased operational costs and environmental impact.
Inefficient demulsifiers: The selection and application of demulsifiers can significantly impact demulsification efficiency. Inadequate demulsifiers or incorrect dosages can result in incomplete separation or prolonged settling times.
Compatibility issues: Some demulsifiers may not be compatible with the emulsion components or the overall process conditions. Compatibility issues can reduce the effectiveness of demulsifiers and hinder the separation process.
Environmental concerns: Traditional demulsification methods may involve the use of chemicals or generate waste products that can have environmental implications.
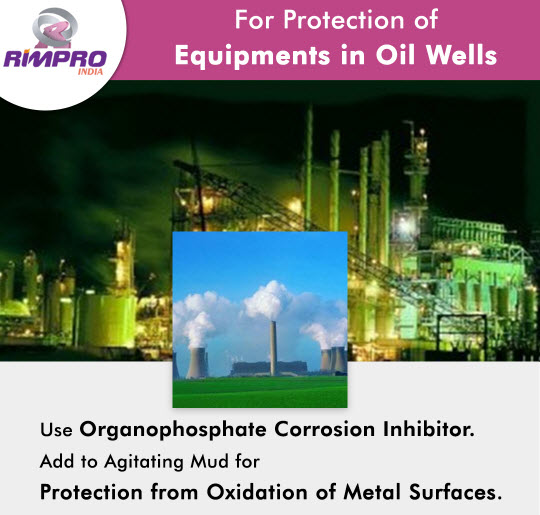
Solutions for Demulsification Problems
Optimal demulsifier selection: Careful evaluation of demulsifiers based on the emulsion composition and characteristics is crucial. Choosing demulsifiers with high efficiency and compatibility with the specific emulsion can significantly enhance the demulsification process.
Proper dosage and mixing: The correct dosage of demulsifiers, along with thorough mixing, ensures effective interaction between the demulsifier and the emulsion. This promotes the destabilization of the emulsion and facilitates quicker separation.
Enhanced mechanical methods: Utilizing mechanical techniques such as centrifugation, filtration, or electrostatic coalesces can aid in demulsification. These methods apply external forces to promote the aggregation and coalescence of dispersed droplets, leading to faster separation.
Temperature and pH adjustments: Adjusting the temperature and pH of the emulsion can influence its stability and demulsification kinetics. Heating the emulsion or altering its pH can disrupt interfacial forces and improve separation efficiency.
Electrostatic methods: Electrostatic methods utilize electrical fields to induce coalescence of emulsion droplets. By applying the appropriate electric potential, charged droplets can be attracted to one another, facilitating their aggregation and subsequent separation.
Application of coalescing agents: Coalescing agents promote the collision and merging of emulsion droplets, aiding in their separation. These agents can be added to the emulsion to accelerate the coalescence process and enhance demulsification efficiency.
Filtration and centrifugation techniques: Employing filtration and centrifugation techniques can physically remove the separated phases from the emulsion. This ensures the extraction of pure oil and water, minimizing residual water content and improving overall product quality.
Continuous monitoring and optimization: Regular monitoring of demulsification processes allows for the identification of inefficiencies or deviations. By continuously optimizing operating parameters, such as demulsifier dosage, mixing intensity, and separation techniques, the overall demulsification efficiency can be maximized.